Production under control
VEGA sensors prove their capabilities in pharmaceutical processes
Pharmaceutical production tools and methods are diverse – they range from mass production to personalised drug manufacture or single-use equipment. Regardless of the task at hand, the demand for flexibility, but also for traceability, is increasing. Only sensors that can be seamlessly integrated into the production process and used flexibly deliver the data required for this. VEGA sensors show how this works in practice.
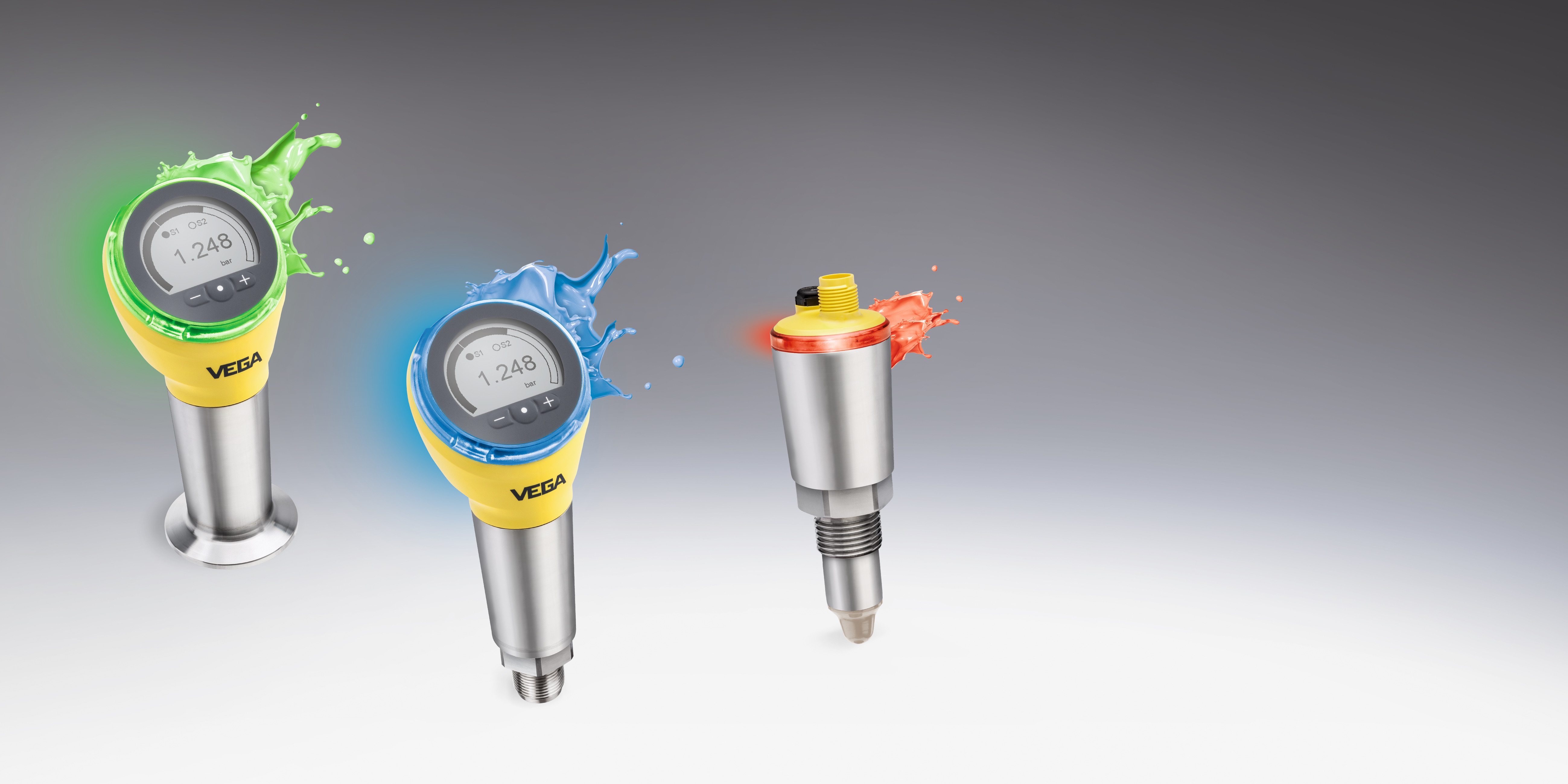
In the biotechnology and pharmaceutical industries, hygiene, repeatability and flexibility are decisive factors for efficient and safe production with a high degree of automation. This reality also affects the measurement technology used. Instrumentation not only has to deliver accurate and reliable measured values, but above all has to be flexible in its application. VEGA sensors meet these requirements in multiple respects. They are durable, extremely robust and highly adaptable to a wide variety of installation situations, even in small vessels or tanks with stirrers or heating coils.
Easy cleaning – safe processes
In complex applications with exceptionally high demands on hygiene, measuring accuracy and speed: the sensors based on the modular system plics® are used. One important characteristic of plics® is its wide range of connection options. This makes it easy to integrate the sensors into existing production systems. For applications involving the hygienic and sterile production of active ingredients, VEGA offers materials specially tailored to the strict requirements of the pharmaceutical industry in accordance with FDA, EG 1935/2004 and the GB standards. The hygienic design meets all standards according to EHEDG and 3-A Sanitary. In terms of design, the sensors are especially characterised by their flush-mounted process fittings and tight, robust housings (IP69K). With their well protected seals, all-metal housings and process-contacting surfaces with a roughness at only 0.38 µm, these VEGA sensors meet all the requirements of the pharmaceutical industry. Conformity and validation is continuously checked by carefully examining all production processes regularly, including individual piece testing as required by GMP regulations.
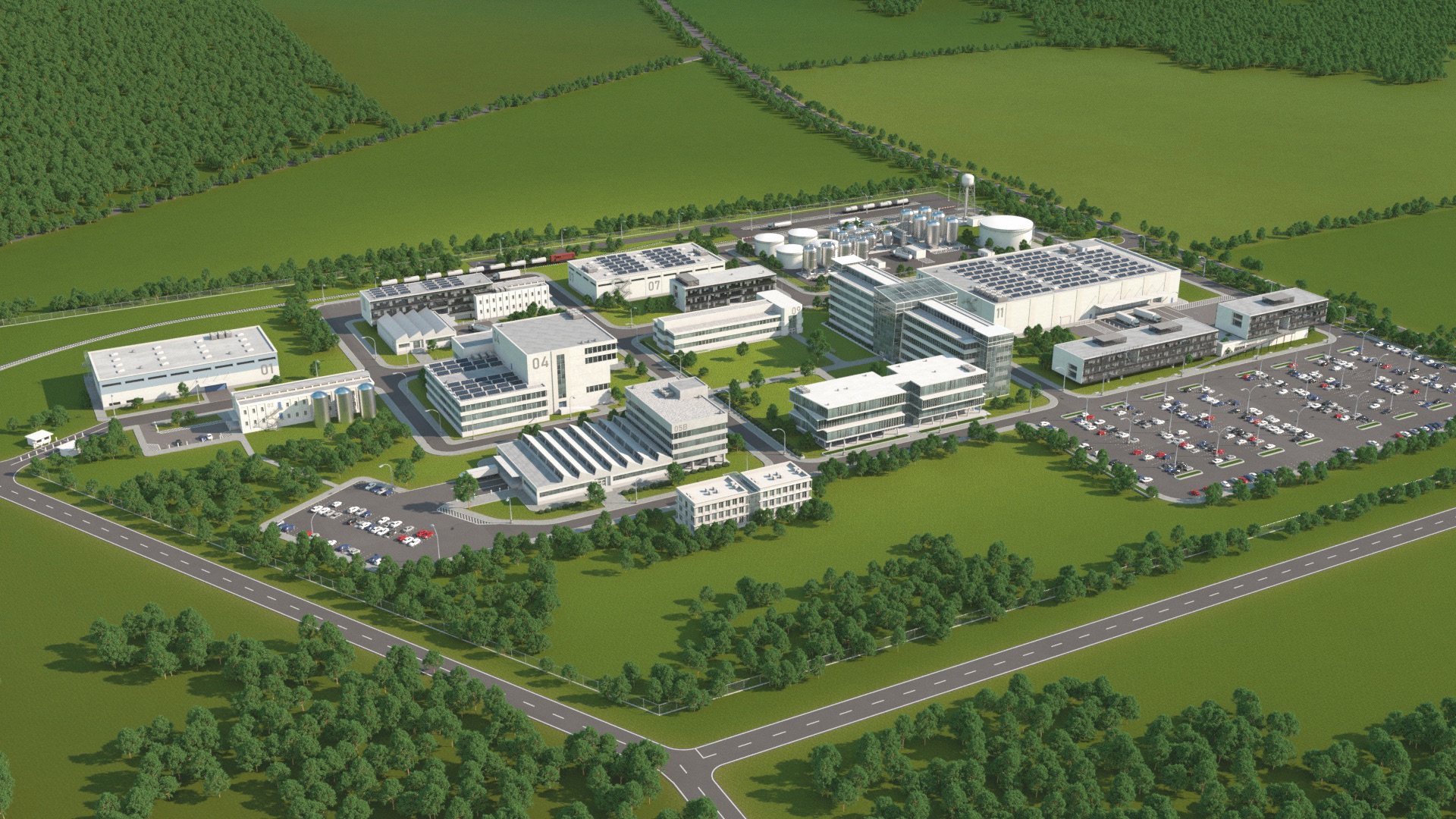
Even during operation, the sensors can be CIP/SIP cleaned up to 2 hours at 150 °C with almost any chemical cleaning agent. This applies to level, pressure and point level sensors. The sensors themselves play an important role in supporting hygienically demanding processes. In many applications they ensure that water, lyes, acids or steam are available in sufficient amounts in the storage tanks and that CIP/SIP processes run smoothly.
Complex measuring tasks
Several application examples show where VEGA sensors are used in pharmaceutical and biotech manufacturing. They are used, for example, for level and pressure measurement in the production of enzymes, proteins and antibodies. To produce modern medicines, it often requires cells or microorganisms to be cultivated in bioreactors. The highest level of hygiene is required here and the containers must be easy to clean. Even minimal contamination with other organisms can cause a reaction to fail.
The processes are mostly so-called fed-batch processes, in which the reactor is completely filled once and only emptied after the reaction or growth time has elapsed. Pressure and level in the reactor must be continuously monitored throughout the entire time in order to obtain a high-quality end product. This is where the radar sensor VEGAPULS 64 is deployed, continuously measuring the level in the bioreactor. Its advantages include a flush-mounted, encapsulated antenna, which is easy to clean, and above all, unaffected by the extreme conditions of the SIP and CIP processes. Another advantage that pays off, especially in day to day batch operation, is that the reactor can be used to its maximum capacity. This is due to the fact that measurement is possible virtually right up to the upper edge of the container.
The sensor also offers these advantages in WFI storage tanks, where non-contact level measurement is particularly important. The radar sensor measures completely up to the top, even in small vessels. Even changing media and process conditions have no affect on the sensor. The narrow beam angle and good focusing of the 80 GHz radar technology – enables easy alignment of the sensor, avoids internals and delivers a pin-point measurement, so to speak.
The VEGABAR 83 pressure transmitter is also frequently used in bioreactors and their interconnected pipelines. What really pays off here is its ruggedness, which the welded, 50 μm-thick alloy diaphragm with aseptic process fitting contributes to. Neither the chemical cleaning cycles or thermal shocks after sterilization can harm the diaphragm. Measuring ranges from -1 ... +1,000 bar and process temperatures between -40 ... +200°C are no problem for the sensor.
The sensor also plays an important role in the production of high-purity water (WFI). The purified water evaporates in the steam separator and is fed into the condenser. Evaporation is effected by a heat exchanger supplied with saturated steam. The pressure inside the steam separator must be kept constant in order to achieve maximum efficiency. The elastomer-free all metallic VEGABAR 83 pressure transmitter measures the gauge pressure in the vapour phase, and its materials are perfectly suited to be in contact the highly pure WFI water.
New sensors for simple process monitoring
In this part of the process, the newcomer among VEGA sensors is also used. For the standard automated auxiliary applications, VEGA have now developed and introduced a new series of pressure sensors with switch functions (VEGABAR) and point level switches (VEGAPOINT). The sensors are very compact, meet all hygienic design requirements according to EHEDG and 3A and comply with the specifications of FDA, EG1935/2004 as well as GB standards.
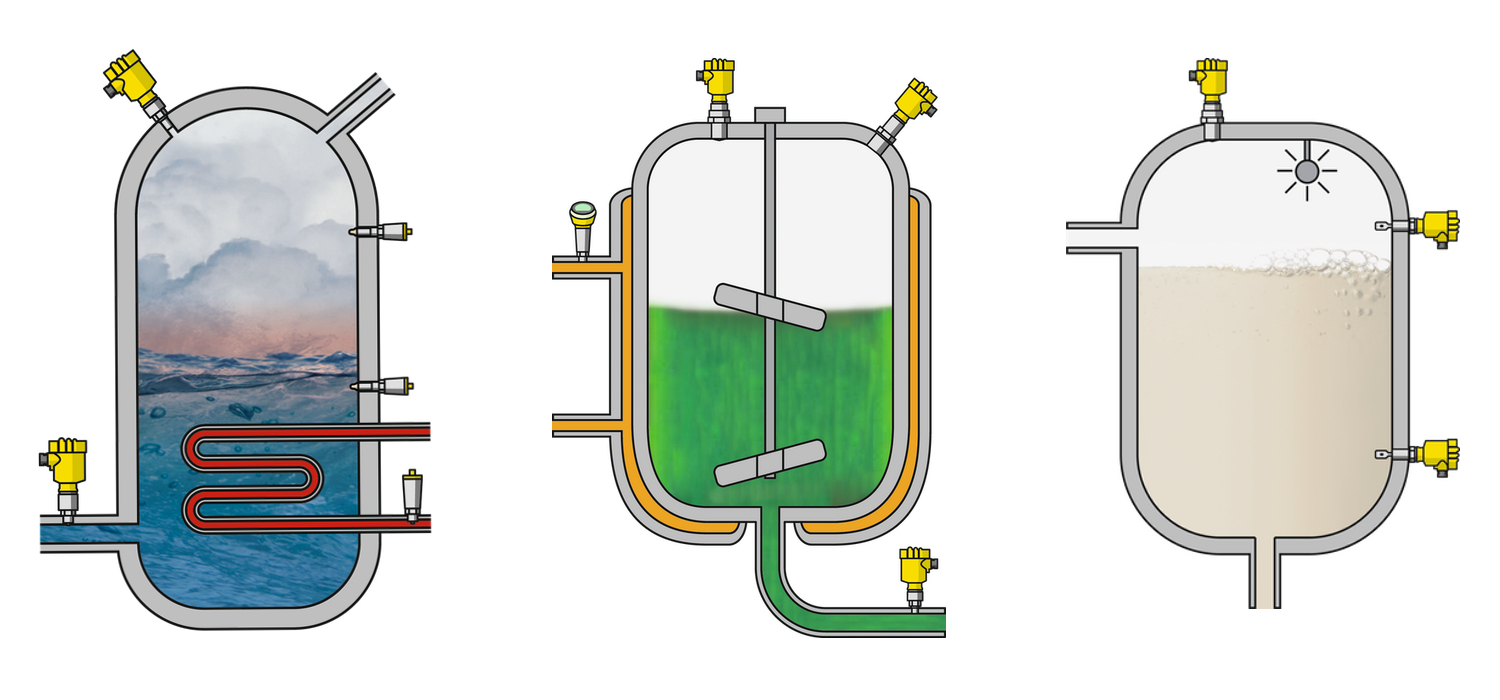
Left | Middle | Right |
---|---|---|
Pressure measurement and level detection in the steam separator | Level and pressure measurement in the bioreactor during the production of enzymes, proteins and antibodies | Level and level detection in the detergent storage tank of the CIP system |
The new series utilises IO-Link communication, which makes sensor exchange very quick and easy, because all settings are stored in the IO-Link master and automatically loaded into any replacement sensor. Besides transmitting the pressure measurements and switch points, the process temperature is also provided. Another aspect: The more flexible a production system is, the more likely it is that contamination will occur. For that reason, all process cycles must be completely traceable. Thanks to IO-Link, not only is it possible to easily integrate VEGA sensors into production control systems, the data collected can also easily be fed to business and laboratory systems.
The so-called 'aqua purificata' evaporated in the steam separator enters the condenser to become high purity water (WFI). Inside the condenser there a cooling system that condenses steam. The feed of cooling liquid is monitored in the pipeline. Point level detection ensures that a sufficient seal of condensate is present to prevent steam from entering the WFI reservoir directly via the feed pipe. The pressure transmitter VEGABAR 29 measures the pressure in the saturated steam line.
Another device of the new series – the pressure sensor VEGABAR 38 – is used in the feed lines of the heating medium as well. It is also equipped with the robust, ceramic CERTEC® measuring cell – so a long service live is guaranteed. And, thanks to its VDMA menu structure and integrated display, the sensor is also characterized by very simple setup and adjustment. This is an important factor, especially with regard to flexibility, e.g. for gathering data from an ongoing process in an uncomplicated way.
VEGAPOINT 21, a capacitive level switch, is also used in this process – it detects the level in the steam separator. This is also a new product series from VEGA that has caused quite a stir, and not only because of its reliable switching in water and steam. These level switches – just like the VEGABAR series mentioned above – are equipped with a 360° bright status display. This allows the condition of the sensor to be seen very clearly, even from a distance. For the user this has major advantages, especially in plants full of nooks and crannies.
Outlook
In conclusion, an example application from a drum coater should be mentioned. A suspension of colour coating or active ingredient is sprayed into the drum via nozzles and distributed evenly there. Reliable level measurement is necessary to ensure that there is enough of the suspension in the storage tank to coat the tablets. While VEGAPULS 64 is used in the storage vessel of the drum to display the measured value directly and visualise the vessel contents via Bluetooth, the capacitive level switch of the new VEGAPOINT 21 sensor series serves as overfill and dry run protection.
The example clearly shows how point level and continuous level sensors from VEGA can work together smoothly in pharmaceutical and biotech processes. Regardless of whether complex requirements or simple measuring tasks are involved, the user can count on a solution that is reliable, long-lasting and flexible.